Navigating the World of Fasteners and Machining: Strategies for Accuracy and Speed
In the elaborate realm of bolts and machining, the quest for accuracy and speed is a continuous challenge that requires careful focus to detail and calculated planning. From recognizing the diverse range of bolt kinds to choosing optimum products that can withstand rigorous needs, each action in the process plays a critical function in accomplishing the wanted outcome.
Understanding Bolt Types
When choosing bolts for a project, recognizing the numerous kinds readily available is crucial for ensuring ideal efficiency and reliability. Bolts come in a wide variety of types, each created for specific applications and demands. Screws are used with nuts to hold materials with each other, while screws are functional bolts that can be made use of with or without a nut, depending on the application. Nuts, on the various other hand, are inside threaded fasteners that friend with screws or screws, providing a protected hold. Washers are crucial for dispersing the tons of the fastener and preventing damage to the product being attached. Additionally, rivets are long-term fasteners that are suitable for applications where disassembly is not needed. Comprehending the distinctions in between these bolt types is necessary for picking the right one for the work, making certain that the connection is strong, sturdy, and reputable. By selecting the suitable bolt kind, you can optimize the efficiency and durability of your project - Fasteners and Machining.
Choosing the Right Products
Recognizing the significance of choosing the ideal materials is extremely important in making sure the ideal efficiency and integrity of the selected fastener types discussed previously. When it pertains to fasteners and machining applications, the product selection plays a vital duty in identifying the general toughness, sturdiness, rust resistance, and compatibility with the desired setting. Different materials offer varying properties that can considerably influence the efficiency of the fasteners.
Common materials utilized for fasteners include steel, stainless steel, aluminum, brass, and titanium, each having its special staminas and weak points. Steel is renowned for its high strength and durability, making it suitable for a broad range of applications. Choosing the appropriate product involves taking into consideration variables such as strength needs, environmental problems, and budget plan restrictions to make sure the wanted efficiency and durability of the fasteners.
Precision Machining Techniques

Along with CNC machining, other precision strategies like grinding, transforming, milling, and drilling play important duties in fastener production. Grinding helps accomplish fine surface area coatings and tight dimensional tolerances, while transforming is often used to create cylindrical components with exact diameters. Milling and exploration procedures are vital for forming and developing holes in bolts, guaranteeing they satisfy precise specifications and feature appropriately.
Enhancing Rate and Performance
To optimize bolt production procedures, it is vital to simplify procedures and apply efficient methods that match precision machining techniques. Automated systems can take care of repeated tasks with accuracy and speed, permitting workers to focus on more facility and value-added tasks. By integrating these techniques, suppliers can attain a balance in between rate and accuracy, eventually improving their competitive edge in the fastener industry.
Quality Assurance Steps
Executing strenuous quality control procedures is critical in making sure additional hints the dependability and consistency of bolt products in the manufacturing process. Quality assurance he has a good point actions incorporate various stages, beginning from the choice of basic materials to the final evaluation of the ended up fasteners. One essential facet of quality assurance is carrying out complete product inspections to validate conformity with specs. This includes assessing variables such as product resilience, toughness, and structure to guarantee that the bolts meet market criteria. In addition, monitoring the machining processes is necessary to copyright dimensional accuracy and surface area finish quality. Using sophisticated innovation, such as automated inspection systems and precision measuring devices, can boost the accuracy and efficiency of high quality control procedures.
Regular calibration of devices and machinery is crucial to keep consistency in production and ensure that fasteners fulfill the necessary resistances. Carrying out strict procedures for recognizing and addressing non-conformities or flaws is vital in protecting against substandard products from going into the market. By establishing a detailed quality assurance structure, manufacturers can maintain the track record of their brand name and provide fasteners that meet the highest possible criteria of performance and toughness.
Final Thought
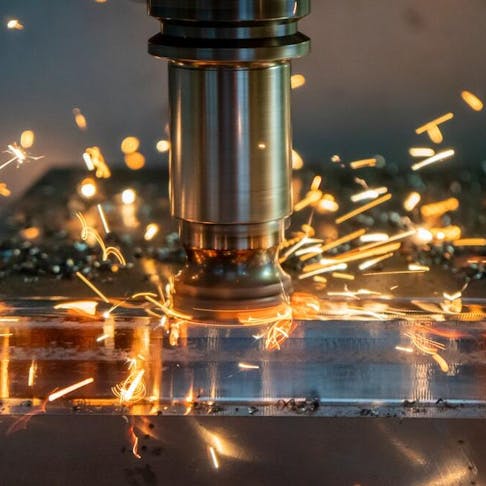
In the intricate realm of fasteners and machining, the mission for accuracy and rate is a perpetual challenge that requires thorough interest to information and calculated preparation. When it comes to bolts and machining applications, the product choice plays a crucial role in figuring out the general strength, resilience, corrosion resistance, and compatibility with the intended environment. Accuracy machining entails numerous sophisticated techniques that make sure the tight tolerances and specs required for fasteners.In enhancement to CNC machining, various other accuracy techniques like grinding, turning, milling, and drilling play important functions in fastener manufacturing.To optimize bolt manufacturing procedures, it is essential to enhance procedures and carry out reliable approaches that match accuracy machining strategies.